Precision Welding: The Art of Seamless Strength
Delivering Durable and Flawless Joints for Every Application
Welding is a cornerstone of modern manufacturing, and when it comes to achieving seamless strength in metal fabrication, precision welding stands as one of the most critical techniques. In industries ranging from aerospace to automotive, construction, and heavy machinery, the quality of welds determines the overall strength, durability, and safety of a product. Precision welding goes beyond just joining two pieces of metal; it involves creating strong, clean, and perfectly aligned seams that enhance the integrity of the final product.
At Zhuoyue Metal Products, we specialize in precision welding, ensuring that every weld we create not only meets but exceeds the stringent requirements of our clients. In this article, we will explore what precision welding is, the techniques involved, its importance in manufacturing, and how it contributes to creating products with superior strength and durability.
What is Precision Welding?
Precision welding refers to welding techniques that are characterized by high accuracy, control, and attention to detail. The goal is to create a weld that is seamless, with minimal distortion and defects, ensuring the strength and functionality of the metal parts. Unlike traditional welding, which may focus on speed or cost-efficiency, precision welding emphasizes fine-tuned control, ensuring that the weld quality remains consistent and up to the highest standards, even in complex or delicate applications.
Key Aspects of Precision Welding:
- High Precision: Achieving tight tolerances and minimizing the margin for error.
- Clean Welds: Ensuring smooth, strong joints with minimal defects such as spatter or porosity.
- Consistency: Maintaining uniform weld quality across multiple pieces or batches.
- Durability: Producing strong joints that can withstand high stresses, temperature changes, and harsh environments.
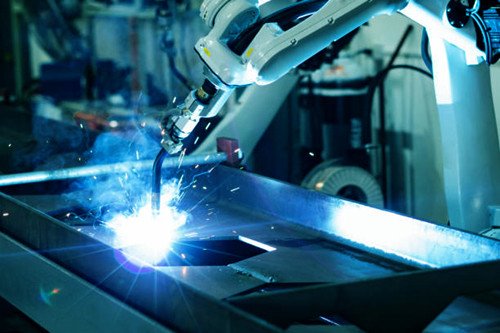
Types of Precision Welding Techniques
Several welding methods can be used in precision welding, each with its own set of advantages depending on the application. The choice of technique depends on factors like material type, thickness, joint configuration, and the required strength of the weld.
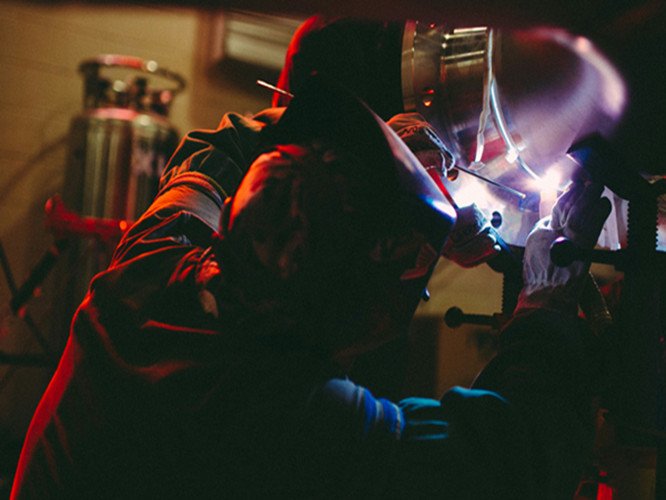
1. TIG Welding (Tungsten Inert Gas Welding)
TIG welding is often considered the most precise welding method. It uses a non-consumable tungsten electrode to produce the weld, with an inert gas (usually argon) used to shield the weld pool from contaminants. This process allows for fine control over the heat and the welding arc, making it ideal for materials that require high precision, such as stainless steel, aluminum, and titanium.
Applications:
- Aerospace components
- Medical devices
- High-performance automotive parts
2. MIG Welding (Metal Inert Gas Welding)
MIG welding, also known as Gas Metal Arc Welding (GMAW), is a faster process than TIG welding and uses a consumable wire electrode to create the weld. While MIG welding is less precise than TIG welding, it can still offer high-quality, clean welds with proper technique. MIG welding is often used for thicker materials and larger production runs, making it a popular choice for manufacturing trailer frames, structural components, and machinery parts.
Applications:
- Automotive production
- Trailer and heavy equipment manufacturing
- General fabrication
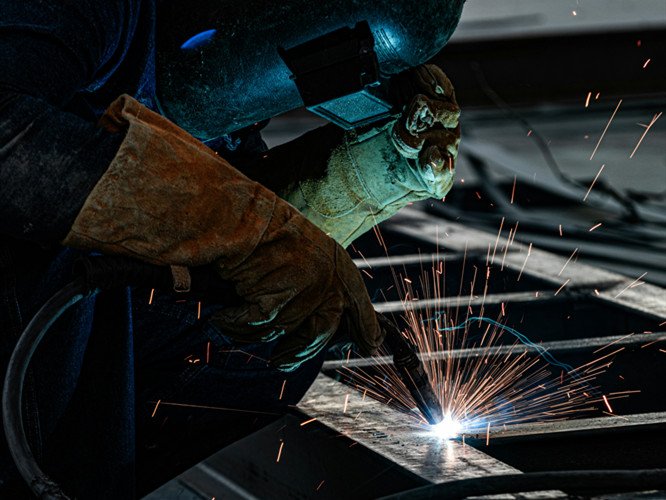
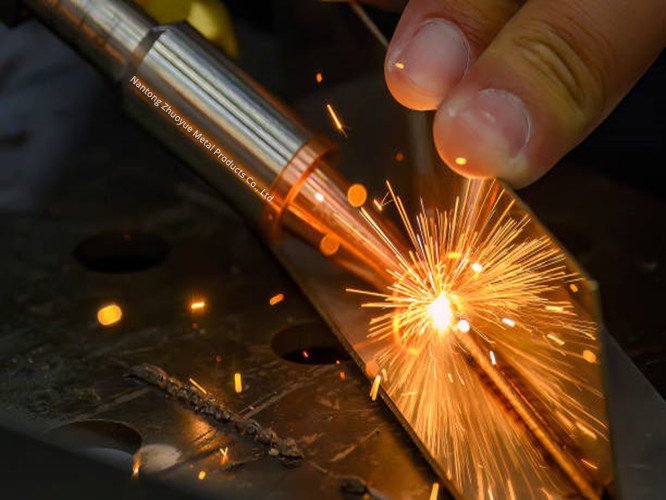
3. Laser Welding
Laser welding is a cutting-edge technique that uses a focused laser beam to create the weld. This process provides an extremely high level of precision and can be used for thin materials and parts with very fine features. Laser welding is known for its speed, minimal heat distortion, and the ability to create high-quality welds in hard-to-reach areas.
Applications:
- Electronics and electrical components
- Medical device manufacturing
- Aerospace and automotive precision parts
4. Spot Welding
Spot welding involves the use of electrical resistance to create heat and join two metal pieces at a specific spot. It is often used in sheet metal fabrication, where two thin pieces of metal are joined together. While spot welding is highly efficient, it is typically suited for joining thinner metals and is commonly used in automotive manufacturing for joining panels.
Applications:
- Automotive body assembly
- HVAC systems
- Electrical components
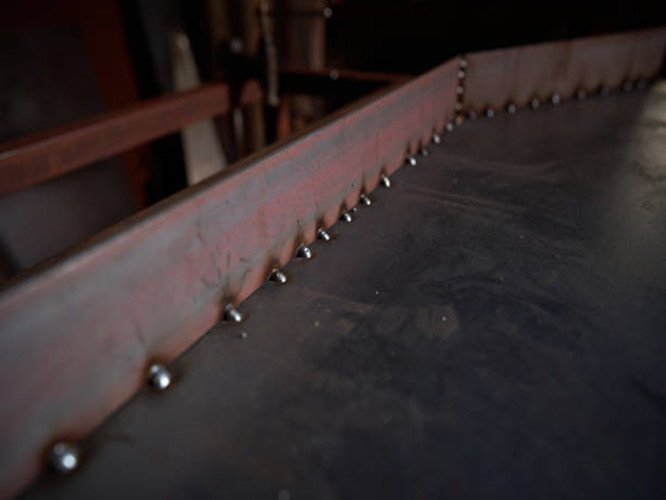
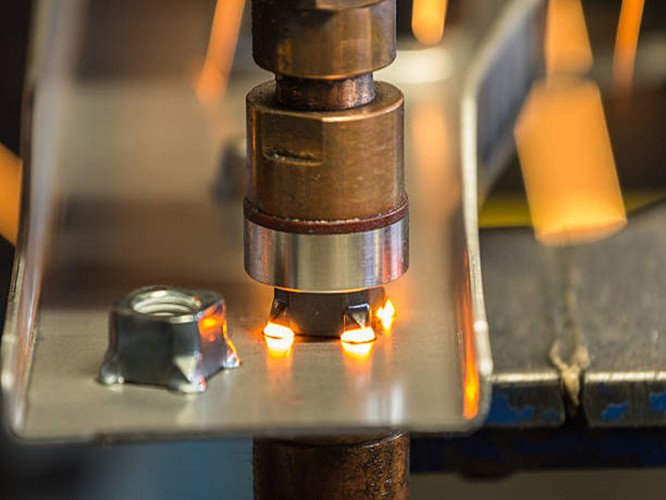
5. Electron Beam Welding
Electron beam welding is a high-precision process that uses a focused beam of electrons to join metal pieces. This process occurs in a vacuum environment, which prevents contamination and produces a very clean and strong weld. Electron beam welding is typically used in industries requiring extremely high-strength welds, such as aerospace and nuclear applications.
Applications:
- Aerospace
- High-end machinery
- Medical device manufacturing
Why Precision Welding Matters
1. Ensuring Structural Integrity
One of the primary reasons for investing in precision welding is to ensure the structural integrity of the welded joint. In industries like automotive, aerospace, and construction, the strength of the weld can make the difference between a safe, long-lasting product and one that fails prematurely.
For instance, in trailer manufacturing, Zhuoyue Metal Products uses precision welding to ensure that the trailer frames can handle heavy loads and extreme conditions. Strong, high-quality welds are essential for ensuring that the frame remains intact under the weight of cargo, ensuring both the safety and durability of the product.
2. Reducing the Risk of Defects
With traditional welding, there is always a risk of defects such as porosity, cracking, or lack of fusion. These defects can weaken the weld and reduce the overall strength of the product. Precision welding minimizes these risks by using highly controlled parameters, ensuring that the weld is uniform and free of defects.
For example, in TIG welding, the welder can precisely control the heat input, which minimizes the risk of warping, distortion, or burn-through. This level of control makes TIG welding an ideal choice for applications that require flawless, defect-free welds, such as medical devices or precision automotive components.
3. Improving Aesthetic Quality
Beyond strength, aesthetics also play a crucial role in many industries, especially in consumer-facing products like automotive parts, appliances, and furniture. Precision welding produces smooth, visually appealing welds with minimal visible seams, making the product more aesthetically pleasing.
For instance, Zhuoyue Metal Products offers high-quality trailer frames that not only perform well but also have clean, smooth welds that look polished and professional. This attention to detail adds value to the final product and enhances the brand’s reputation.
4. Minimizing Material Waste
Precision welding is also an efficient process when it comes to material usage. Because the welds are accurate and precise, there is less need for rework or additional material to compensate for inaccuracies. This reduces material waste and overall production costs, which is particularly important for manufacturers looking to maintain a competitive edge.
In mass production, such as the manufacturing of structural steel components or automotive parts, reducing waste through precision welding translates to higher efficiency and lower costs in the long run.
5. Customizability
Precision welding techniques, such as laser welding or TIG welding, offer high levels of customizability, allowing manufacturers to create unique, complex geometries that would be difficult to achieve with other methods. This is particularly beneficial for industries that require specialized or bespoke components, such as medical devices or aerospace equipment.
For example, Zhuoyue Metal Products can use precision welding to fabricate custom metal parts for industries with stringent requirements, such as creating bespoke trailer frames designed to meet specific load-bearing and dimensional standards.
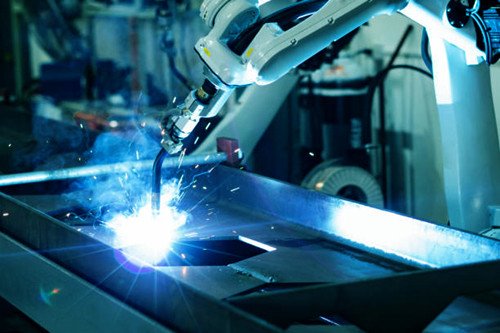
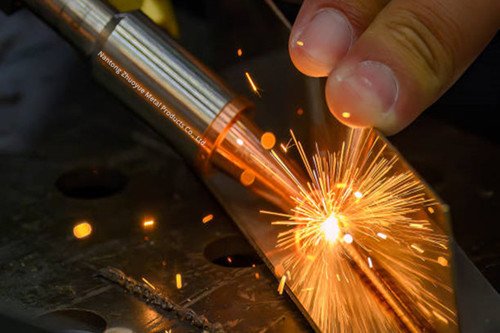
Applications of Precision Welding Across Industries
1. Automotive Industry
In automotive manufacturing, precision welding is crucial for creating safe, high-performance vehicles. From welding body panels to assembling engine components, the strength and precision of the welds directly impact the safety and durability of the vehicle.
2. Aerospace Industry
The aerospace industry demands the highest level of precision in welding to ensure the safety and reliability of aircraft. Components like turbine blades, wing structures, and fuel tanks all rely on precision welding to withstand extreme conditions and high stress.
3. Medical Device Manufacturing
In the medical device industry, where reliability and safety are paramount, precision welding is used to produce small, intricate components like surgical instruments, implants, and medical devices. Clean, defect-free welds are essential to prevent any risk of contamination or failure.
4. Construction and Heavy Equipment
In heavy-duty industries like construction and manufacturing, precision welding is used for critical components such as steel beams, machinery frames, and load-bearing structures. Strong, precise welds ensure that these parts can handle the rigorous demands of the job site.
5. Energy and Power Generation
Precision welding is essential in the energy sector for manufacturing components such as heat exchangers, pressure vessels, and turbine components. These parts must withstand high temperatures and pressures, and precision welding ensures their reliability over time.
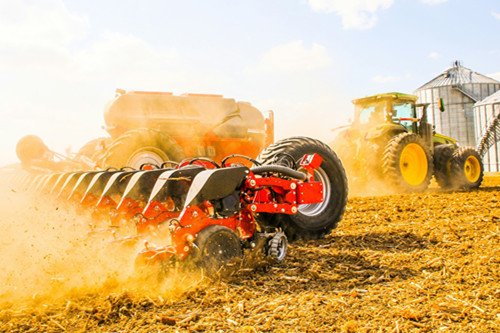
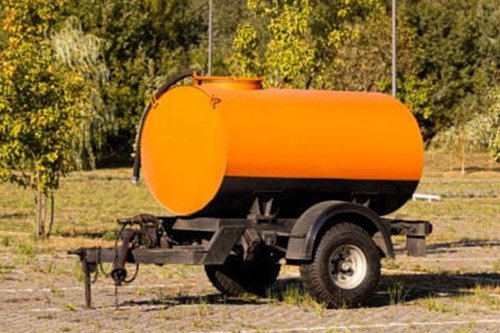
Conclusion
Precision welding is an art that requires skill, experience, and attention to detail. Whether you are producing automotive parts, aerospace components, or heavy machinery, the strength, durability, and quality of your welds directly affect the overall performance of your product. At Zhuoyue Metal Products, we utilize advanced welding techniques to deliver welds that meet the highest standards of strength, precision, and reliability.
By investing in precision welding, manufacturers can enhance the integrity, safety, and performance of their products, while also reducing defects, material waste, and production.
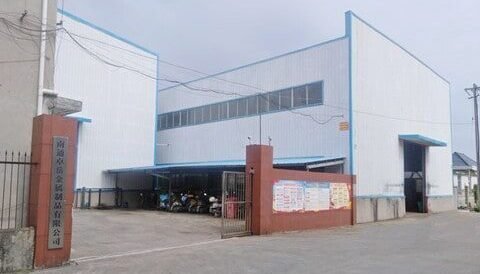